As a mature bulk material conveying equipment, the belt conveyor parts have formed a standard form, and the form has been revised several times according to the problems arising in production and use, and has evolved into the now well-known DTII (A) type [1]. In the system design, DTII (A) type belt conveyor has reasonable structure and simple manufacturing, and the unified standard has greatly simplified the design and manufacturing process, and its shape is widely recognized by the belt conveyor industry. In the actual use of long distance, large capacity and large bandwidth belt conveyor, DTII (A) type belt conveyor roller set has appeared the phenomenon of wear tape, which is caused by the gap between the middle roller and side roller of the roller set, and the tape non-working surface repeatedly passes through the roller gap in the process of large capacity and long distance transportation. In the same position for a long time suffer from extrusion, scratch, make the tape wear a deep groove, until early scrap, not only reduce the safety factor of the conveying system, but also make the user use cost increase.
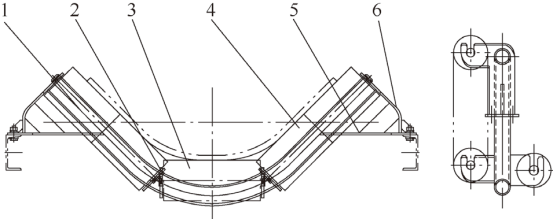
1. "U" shaped roller frame 2. middle pillar 3. middle roller 4. side roller 5. connecting plate 6. side pillar
GCS " offset U" idler set, the middle roller of the normal roller set is offset in the opposite direction of the tape running, and the side rollers are close to the vertical center of the roller set, so that the middle roller and the side rollers are partially overlapped along the tape running direction, which cleverly solves the problem that the gap between the middle roller and the side rollers of the roller set scratches the tape.
The crossbeam of offset U-roller set is changed to round tube, which makes the new front tilting roller set lighter in the same force condition, and the card plate is set at the groove of the side pillar of the roller frame to prevent the roller from falling off.
The offset trough-shaped roller set adopts the steel tube "U" shaped frame body, heats the seamless steel tube, bends it to the design shape by the bending machine, welds the middle pillar and side pillar to the design position of the "U" shaped frame body respectively, sinks the "U" shaped frame as a whole, and then bends it to the design position of the "U" shaped frame body. The "U" shaped frame is sunken as a whole and connected to the middle frame of the belt conveyor through the connecting plate. This type of roller frame reduces the overall center of gravity of the roller group and minimizes the overturning moment of the roller group caused by the frictional resistance of the tape.
About 50% of the tape and material weight are carried by the middle roller. The overturning moment generated by the tape friction resistance along the running direction of the belt conveyor is offset by the moment generated by the tape and material weight carried by the middle roller, which minimizes the overall moment of the roller group and maintains the stability of the roller group. The moment of the rollers as a whole is reduced to the minimum, so as to keep the stability of the stress state of the rollers and avoid the phenomenon of "collapse" of the rollers.
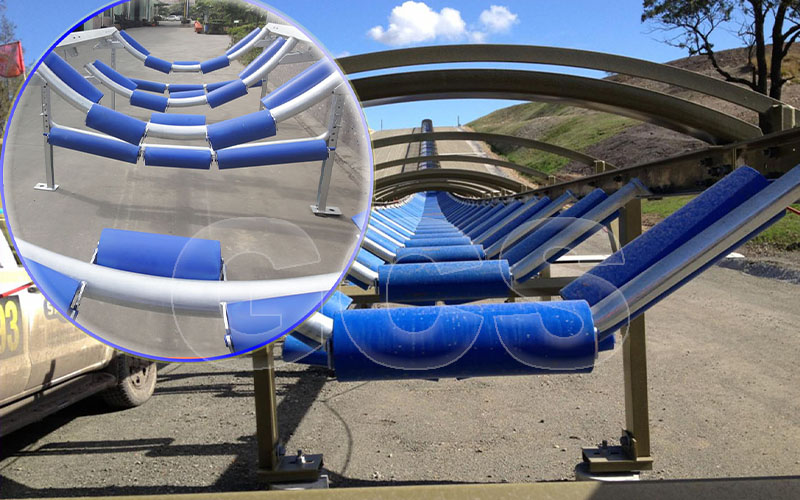
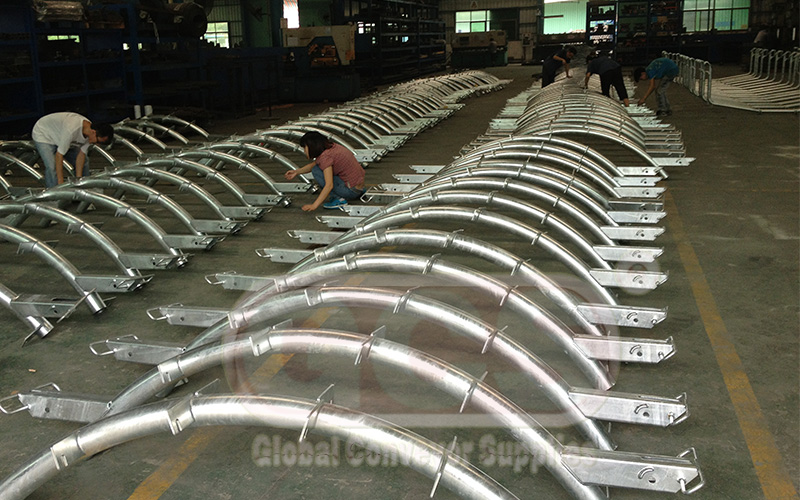
Successful Cases
GCS reserves the right to change dimensions and critical data at any time without any notice. Customers must ensure that they receive certified drawings from GCS prior to finalizing design details.
Post time: Feb-08-2023